专利名称:生产钕铁硼永久磁铁的方法本发明涉及一种花费不大生产钕铁硼永久磁铁合金的方法。众所周知,用稀土金属、电解铁、电解钴、纯硼或铁硼合金作原料,经熔化、粉碎、在磁场中压制和烧结这样一种方法,可以制取稀土金属铁硼永久磁铁-一种新型优质永久磁铁(日本专利公开59-215460)。但这种传统的熔炼法采用价昂的稀土金属,因而成本高。最近有人提出了一种所谓还原法作为熔炼法的另一种可供选择的方法。例如日本专利公开59-219404公开了一种通过还原反应生产稀土铁硼永久磁铁合金的方法,该方法包括下列工序将稀土氧化物粉料、铁粉、铁硼合金粉和钴粉与还原稀土氧化物粉料所需还原剂按化学计算量的2~4倍(以重量计)的金属钙或氢化钙进行混合,将它们在900~1200℃下的惰性气体气氛中加热,用水清洗反应产物,以除去反应副产物。还有,日本专利公开59-177346公开了在还原法中采用助熔剂降低低熔点熔体粘度的作法。上述一般还原法(日本专利公开59-219404)需要长时间水洗以除去还原反应产物氧化钙。对富铁的稀土元素铁硼合金来说,在水洗工序中有激烈的氧化反应产生,这增加了生成的合金中的含氧量,因此难以稳定地获取磁性能良好的磁铁合金。同时,要通过水洗完全除去氧化钙非常困难,且残留的氧化钙在烧结工序中降低永久磁铁合金的可烧结性,从而劣化所得永久磁铁的磁性能。此外,普通采用助熔剂的还原法(日本专利公开59-177346)并不能将所得合金中的钙含量降低到可容许的水平。最近有人提出一种生产钕铁硼磁铁合金用的钕铁或钕铁硼母合金的生产方法,该方法是将氟化钕、钙、铁必要时氧化硼等原料与作为助熔剂的氯作钙一起加入铁容器中,将它们在750至1000℃下的非氧化气氛中熔化,以便将氟化钕还原成钕(日本专利公开61-84340)。但这种方法不能提供钙含量极低的钕铁硼合金。因此,用这些母合金制造出来的磁铁不可避免地具有较高的能降低磁性能的钙含量。此外,由于母合金的组成与最终的永久磁铁大不相同,因而需要加入铁和硼以使合金改变为所需的组成。因此本发明的一个目的是解决普通方法中的这些问题,从而提供钙和氧含量极低因而磁性能优异的钕铁硼永久磁铁合金。计对上述目的进行深入研究的结果,本发明者同人发现,由于钙对钕的亲合力强,上述现有技术的母合金不可避免地会含有大量的钙;将钕含量降低到25~50重量%的程度不仅可以降低生成的合金的钙含量,而且还可提供可直接制成钕铁硼磁铁的合金。本发明就是以这个发现为基础的。
就是说,本发明生产钕铁硼永久磁铁合金的方法是往氟化钕、铁和硼(或铁硼合金)组成的混合物中加入作为还原剂的金属钙、氢化钙或它们的混合物,再加入作为助熔剂的氯化钙、氯化钠或氯化钾中的至少一种,再将由此得出的混合物在1000~1300℃下的惰性气体气氛中,或在还原气体气氛中,或在大体上真空中熔化,从而还原氟化钕以制取主要由25.0~50.0重量%的钕、0.3~5.0重量%的硼、其余大体上为铁和极少量的钙所组成的合金。原料中可含有氟化镝,使生成的合金中含0.5~15重量%的镝。
图1是根据本发明的一个实施方案制取的钕铁硼永久磁铁的钕含量与其磁性能的关系曲线。
图2是根据本发明的另一个实施方案制取的钕铁硼永久磁铁的硼含量与其磁性能的关系曲线。
作为稀土组份的原料,采用了氟化钕,将其按这样的量与铁和硼(或铁硼合金)混合;使得还原反应之后的组成大致为25.0~50.0重量%的钕、0.3~5.0重量%的硼,其余为铁。要制备主要由25.0~50.0重量%的钕、0.5~15重量%的镝、0.3~5.0重量%的硼、0.05~5.0重量%的铌、其余为铁组成的合金时,原料中还应含有氟化镝和铌或铁铌合金。
氟化钕在加热过程中开始时是在大致800℃下由还原剂还原,在1000~1300℃下完全还原。还原剂的量应为完成还原所需的按化学计算量(以重量计)的1.0倍或以上。但还原剂最好不过量,因为这样会提高合金的生产成本,而且还增加生成合金中的钙含量。因此还原剂实际用量的上限为4.0倍(以重量计)。还原剂量最好为1.25~2.0倍(以重量计)。附带说一下,当原料中含氟化镝时,它也和氟化钕一样被还原。
经还原的钕和镝(如有的话)与铁、硼(或铁硼合金)和铌(或铁铌合金,如有的话)熔成合金。此工艺中生成的氟化钙副产品形成熔渣。氟化钙的熔点高达1360℃左右,因而很难在1000~1300℃温度下将熔渣从合金中分离出来。
本发明最重要的特点是作为助熔剂的氯化钙、氯化钠和氯化钾中至少其中一种的加入;其目的是降低熔渣熔点以利以熔渣从合金中的分离。氯化钙的熔点约为770℃,氯化钠约为800℃,氯化钾约为780℃,加入这些助熔剂混合物之后,熔渣就更易于在1000℃或稍高的温度下从上述组成的合金中分离出来。助熔剂的加入量为还原反应生成的氟化钙化学计算量的0.05~4.0倍(以克分子计)。当助熔剂量少于0.05倍(以克分子计)分,降低不了熔渣的熔点,结果使熔渣不能充分从合金中分离。另一方面,当助熔剂量高于4.0倍(以克分子计)时,助熔剂对原料的百分比值(特别是体积比)就过高,从而使合金的生产效率不太高。此外,采用过量的助熔剂会增加合金的生产成本和从熔渣转移到合金中的钙量。助熔剂以克分子计的使用量最好取0.5~3.0倍。
作为助熔剂,氯化钙、氯化钠和氯化钾中任何一种都具有分离作用。但加入两种或两种以上上述助熔剂混合物,其分离效果与只加入一种助熔剂成分的效果相等或更好。
本发明的第二要点是氟化钕,必要时氟化镝、铁和硼,还有必要时铌(或铁铌合金)的用量应达到这样的程度,使得氟化钕和氟化镝(如有的话)经还原之后,合金的组成可成为25.0~50.0重量%的钕、0.5~15.0重量%的镝(如有的话)、0.3~5.0重量%的硼、0.05~5.0重量%的铌(如有的话),其余为铁。就是说,钕的量远低于与铁形成类低共熔体所需的量。因此熔化25.0~50.0重量%的钕加铁,比熔化它们的类低共熔体需要高得多的温度。尽管提高加热温度通常没有好处,但用钙还原剂进行还原直接生产具有上述组成的钕铁硼合金却有好处,因为会得出钙含量极低(通常为0.1重量%或更低)的合金,这是我们杰出的发现,生成合金中的钙含量最好为0.06重量%或更低。
上述组成范围可提供磁性能优异的永久磁铁。具体地说,钕应为25.0~50.0重量%。当钕低于25.0重量%时,不能提供足够的矫顽磁力,而超过50.0重量%时,剩余磁通密度低。钕的量最好为30~40重量%。图1就是这方面的例子,这是含1.3重量%硼、其余为铁的钕铁硼合金的磁性能。部分钕可用镝代替。加镝的话,镝含量以0.5~15.0重量%为宜,低于0.5重量%则矫顽磁力得不到充分改善,超过15.0重量%则会降低合金的剩余磁通密度。硼应取0.3~0.5重量%,低于0.3重量%则不能获得足够的剩余磁通密度和矫顽磁力,而且居里温度Tc低;高于5.0重量%则剩余磁通密度低。硼的量最好为0.6~2.0重量%。图2就是这方面的一个例子,这是含36.0重量%钕其余为铁的钕铁硼合金的磁性能。此外,还可以加入0.05~5.0重量%的铌。当铌含量低于0.05重量%时,基本上还觉察不出矫顽磁力有什么提高,而当超过5.0重量%时,合金的剩余磁通密度下降,且产生不希望有的相。
因此本发明的特征在于提供组成完全对应于所期望的永久磁铁的组成的合金。其所以需要使熔渣从合金中有效分离是为了降低熔渣的熔点,使其更易于维持熔融状态。为此,加入上述助熔剂就可以见效。同时需要使得出的钕铁硼合金处于熔融状态。只有当这两个条件都得到满足时,合金才能很好从熔渣中分离出来。
根据我们研究,上述组成的合金,在温度低于1000℃下不熔化,使得合金不能从熔渣中分离出来。因此本合金应在1000℃或更高的温度下熔炼,使其可以从熔渣中分离出来。所以加热温度应等于或高于1000℃。为使分离更确实地进行,加热温度最好等于或高于1050℃。另一方面,若加热温度过高,大量杂质会从装有原料的坩埚中跑进生成的合金熔体中。这样就会消耗太多能量。因此从经济观点看,也不选用过高的温度。所以加热温度有自己的上限,即1300℃。这样,加热温度应在1000~1300℃,最好在1050℃~1300℃。加热时间10分钟或以上就足够了,而加热30分钟或以上可以确保分离。
在本发明的条件下形成的任何熔渣,其熔点是低于1000℃的。因此,在1000~1300℃下加热,熔渣就熔化,从而使比重较大的合金沉到容器底部,同时比重较小的熔渣浮在合金上。
附带说一下,用还原法在低于1000℃的加热温度下从合金中分离熔渣并不是不可能的。众所周知,钕铁二元合金的低共熔温度约为640℃。因此可这样选取氟化钕对铁或铁硼合金的比值,使生成的合金熔体具有75重量%钕和25重量%铁的钕铁二元低共熔体组成。钕量选取大于本发明的规定量时,生成的合金可在低于1000℃的加热温度下,具体地说在700~900℃下从熔渣中分离出来。但在这种情况下就会出现两个大问题其中一个问题是,由于合金成分中含有过量的钕,分离出来的合金中不可避免地含有大量来自还原剂溶解在合金中的钙。另一个问题是,鉴于得出的合金的组成与作为永久磁铁想获取的组成大不相同,为提供永久磁铁用的合金,需要再熔炼来调节合金的组成。这会大大影响永久磁铁产品的磁性能及其生产成本。
恰恰相反,本发明生产合金的方法的特点是生产成本低,因为这种方法提供的合金,其组成与所期望的永久磁铁的组成完全一样,而且这种合金的制备方法有可能使合金中的钙含量最低。这种合金可用粉末冶金法制成永久磁铁,该方法是将合金粉碎,用模具将合金粉压制,再经过烧结和热处理。此外,由于用本发明制备出来的合金比起具有低共熔组成的钕铁合金,钕含量小,且前一种合金中以固溶液的形式存在的钙,含量极小,因而基本上对磁性能没有不良影响。同样的理由,合金中的氧含量比低共熔组成中的小。由于本发明具有上述特点,因此本发明的方法能以低成本生产出磁性能优异的钕硼铁永久磁铁合金。
下面再谈谈生产本发明的永久磁铁合金所用的原料。氟化钕可采用市上出售的粒度100目以下的品种。其纯度(钕在总稀土元素中的含量)最好为95重量%或以上。氟化镝也可采用市面出售的100目以下的品种。铁基本上可采用松散状的,但为顺利完成其与还原过的钕元素熔成合金的过程,宜采用粉状的,且最好大约在32目以下。其纯度可取与市面出售的纯铁同一等级的。至于硼,可采用市面出售的约10目以下的纯硼,也可采用粉状的。在某些情况下,可采用市面出售的氧化硼。这时应另外加入还原剂所加入的氧化硼所需量的还原剂。在这种情况下,氧化硼的还原反应会生成小量的氧化钙。鉴于氧化钙起提高熔渣熔点的作用,因此是不希望它存在的。然而,由于用本发明的方法制备出来的合金,其硼含量小达0.3~5.0重量%,因而往熔渣中加氧化硼所生成的一定比例的氧化钙,其量非常小,基本上对本发明生产方法各条件下合金从熔渣中的分离过程没有有害的影响。此外,从经济的观点看,采用市面出售的铁硼合金比采用纯硼或氧化硼更有好处。铁硼合金可采用松散状的,但与铁同一个理由,最好采用约32目以下的粉料。
铌最好采用铌铁合金或铁铌合金,可取任何形状,松散状或粒状。但与铁同一个理由,最好采用32目以下的粒料。
还原剂可采用市面出售的金属钙或氢化钙,可取任何形式,约20目以下的粉料或粒料,其纯度最好为99%或以上。
助熔剂可单独或联合使用市面出售的氯化钙、氯化钠或氯化钾,最好将其强力加热,以便在使用前彻底清除其中的水分。
下面再谈谈本发明生产永久磁铁合金的方法所使用的容器。原料装料和反应所使用的容器可以是铁制的或不锈钢制的。为尽量抑制熔融合金与容器材料之间的反应,可在容器内壁上涂氮化硼等。此外,容器还可用钨或钽制成,因为它们防止与含钕的熔融合金发生反应的能力优异。再有,由诸如氮化硼和氮化铝等陶瓷材料制成的容器对熔融合金的反应能力较弱,因而适用于本发明的方法。
本发明方法用的原料应具有所规定的成分,将原料在例如V型混合机中混合,将得出的混合物装进上述容器中,加热,以便将生成的合金从熔渣中分离出来。回收合金时令容器倾斜将合金注入锭型中。合金的收集也可以在容器底部开个小孔,打开小孔进行。当采用对熔融合金的反应较小的陶瓷容器时,可将容器冷却到室温,同时令分离了的合金和熔渣留在容器中,稍后再清除。
采用铁质容器时,容器与生成的合金之间可能会发生反应。在这种情况下,可在完成还原反应之后将容器加热到这样的温度,使得只有助熔剂熔化,然后将熔融的助熔剂从容器中除去。接着将容器浸入水、酒精或酒精水溶液中,或用水、酒精或酒精水溶液清洗,以彻底清除残留的助熔剂。在真空的恒温控制烘炉中干燥过后,往其中通氢气,使合金吸收气体。这样,松散状的合金就变为粗粒料。然后用氩气吹除氢气,并在600℃或以下加热粒料,以清除氢气。这样就得出藉氟化钕和氟化镝(如有的话)的还原反应制备的合金。
下面通过实例更详细介绍本发明的内容。
例1准备好169.4克的氟化钕粉、63.3克10目以下的金属钙(所需按化学计算量的1.25倍)、193.9克32目以下的铁粉、22.1克32目以下的铁硼合金粉(20.4重量%硼、其余为铁)和140.0克的氯化钙(应生成的氟化钙按化学计算的克分子的1.0倍),将这些原料在V型混合机中混合,以制取588.7克的母料。将此母料装入不锈钢容器中,在氩气气氛中在1200℃下加热,历时1小时。从熔渣中分离出得出的合金之后,令容器倾斜,使合金流入锭型中。于是得出327.5克合金。对合金成分分析的结果表明,该合金含35.8重量%的钕、1.29重量%的硼、0.02重量%的钙,其余为铁。氧含量为百万分之50。
将该合金粉碎,再进一步用喷磨机磨碎,以提供平均粒度为3.0微米的细粉料。然后将此粉料在10千奥斯特的磁场中在2吨/平方厘米下压制,再把得出的绿色物体在1000℃下的氩气气氛中烧结1小时。最后将烧结过的物体在600℃下热处理1小时。对得出的样品就其磁性能进行测定的结果表明,其剩余磁通密度4πIr=12.1千高斯,矫顽磁力iHc=11.0千奥斯特,最大能量乘积〔BH〕最大=34.5兆高斯奥斯特。该样品含百万分之4500的氧和0.02重量%的钙。
例2准备好182.0克氟化钕粉、108.8克10目以下的金属钙(所需化学计算重量的2.0倍)、166.5克32目以下的铁粉、19.4克32目以下的铁硼合金粉(20.4重量%的硼,其余为铁)和150.4克的氯化钙粉(应生成的氟化钙按化学计算的克分子的1.0倍),将这些原料在V型混合机中混合,以制备627.1克母料。将此母料装入不锈钢容器中,在1050℃下氢气气氛中加热2小时。从熔渣中分离出生成的合金后,令容器倾斜,使合金流入锭型中。于是得出309.4克合金。对合金成分进行分析的结果表明,该合金含40.8重量%的钕、1.20重量%的硼、0.03重量%的钙,其余为铁。氧含量为百万分之60。
按例1同样的方式将此合金制成永久磁铁测定其磁性能。结果,其剩余磁通密度4πIr为11.5千高斯,矫顽磁力iHc为14.0千奥斯特,最大能量乘积〔BH〕最大为31.0兆高斯奥斯特。该样品的氧含量为百万分之4800,钙含量为0.03重量%。
例3准备好139.5克氟化钕粉、65.6克氢化钙粉(所需按化学计算重量的1.5倍)、209.1克32目以下的铁粉、4.5克10目以下的纯硼粉和151.8克的氯化钠粉(应生成的氟化钙按化学计算的克分子的2.5倍),将这些原料在V型混合机中混合,以制备570.5克的母料。将此母料装入氮化硼容器中,在1300℃下的氩气气氛中加热1小时。从熔渣中分离出生成的合金之后,令容器倾斜,使合金流入锭型中。于是得出307.3克合金。对合金成分进行的分析表明,该合金含31.5重量%的钕,1.39重量%的硼、0.01重量%的钙,其余为铁。氧含量为百万分之45。
按例1同样的方式将此合金制成永久磁铁,测定其磁性能。结果,其剩余磁通密度4πIr为12.8千高斯,矫顽磁力iHc为7千奥斯特,最大能量乘积〔BH〕最大为38.4兆高斯奥斯特。该样品的氧含量为百万分之4000,钙含量为0.01重量%。
例4准备好167.4克氟化钕粉、52.5克氢化钙粉(所需按化学计算重量的1.0倍)、229.0克32目以下的铁粉、4.9克10目以下的纯硼粉和325.6克的氯化钾粉(应生成的氟化钙按化学计算的克分子的3.5倍),将这些原料在V型混合机中混合,以制备779.4克母料。将此母料装入钽容器中,在1000℃下的大体上真空中加热4小时。从熔渣中分离出生成的合金之后,令容器倾斜,使合金流入锭型中。于是得出345.0克合金。对合金成分的分析表明,该合金含33.6重量%的钕,1.37重量%的硼,0.02重量%的钙,其余为铁。氧含量为百万分之50。
按例1同样的方式将此合金制成永久磁铁,测定其磁性能。结果,其剩余磁通密度4πIr为12.5千高斯,矫顽磁力iHc为9.2千奥斯特,最大能量乘积〔BH〕最大为36.7兆高斯奥斯特。该样品的氧含量为百万分之4300,钙含量为0.02重量%。
例5准备好127.1克的氟化钕粉、66.5克10目以下的金属钙(所需按化学计算重量的1.75倍)、145.4克32目以下的铁粉、16.6克32目以下的铁硼合金粉(20.4重量%的硼、其余为铁)、157.5克的氯化钾粉(应生成的氟化钙按化学计算的克分子的1.5倍)和83.0克的氯化钠(应生成的氟化钙按化学计算的克分子的1.5倍),将这些原料在V型混合机中混合,以制备596.1克母料。将此母料装入不锈钢容器中,在1150℃下的氩气气氛中加热2小时。从熔渣中分离出生成的合金之后,令容器倾,使合金流入锭型中。于是得出245.5克合金。对该合金成分的分析表明,该合金含35.7重量%的钕,1.29重量%的硼,0.02重量%的钙,其余为铁。氧含量为百万分之55。
按例1同样的方式将此合金制成永久磁铁,测定其磁性能。结果,其剩余磁通密度4πIr为12.2千高斯,矫顽磁力iHc为10.5千奥斯特,最大能量乘积〔BH〕最大为35.0兆高斯奥斯特。该样品的氧含量为百万分之4500,钙含量为0.02重量%。
例6准备好111.6克的氟化钕粉、26.2克氢化钙粉(所需按化学计算重量的0.75倍)、25.0克10目以下的金属钙粉(所需按化学计算重量的0.75倍)、124.6克32目以下的铁粉、2.7克10目以下的纯硼粉和97.2克氯化钠粉(应生成的氟化钙按化学计算的克分子的2倍),将这些原料在V型混合机中混合,以制备387.3克母料。将此母料装入氮化硼容器中,在1100℃下的氩气气氛中加热4小时。从熔渣中分离出生成的合金之后,令容器倾斜,使合金流入锭型中。于是得出202.5克合金。对合金成分的分析表明,该合金含38.4重量%的钕,1.28重量%的硼,0.03重量%的钙,其余为铁。氧含量为百万分之58。
按例1同样的方式将该合金制成永久磁铁,测定其磁性能。结果,其剩余磁通密度4πIr为11.8千高斯,矫顽磁力iHc为12.5千奥斯特,最大能量乘积〔BH〕最大为32.8兆高斯奥斯特。该样品的氧含量为百万分之4700,钙含量为0.03重量%。
例7准备好83.7克氟化钕粉、31.3克10目以下的金属钙粉(所需按化学计算重量的1.25倍)、95.8克32目以下的铁粉、11.0克32目以下的铁硼合金粉(20.4重量%的硼,其余为铁)、55.3克的氯化钙粉(应生成的氟化钙按化学计算的克分子的0.8倍)、29.2克氯化钠粉(应生成的氟化钙按化学计算克分子的0.8倍)和37.2克氯化钾粉(应生成的氟化钙按化学计算克分子的0.8倍),将这些原料在V型混合机中混合,以制备343.5克母料。将此母料装入氮化硼容器中,并在1200℃下的氩气气氛中加热4小时。从熔渣中分离出生成的合金之后,令容器倾斜,使合金流入锭型中。于是得出161.4克合金。对此合金成分的分析表明,该合金含35.7重量%的钕,1.30重量%的硼,0.02重量%的钙,其余为铁。氧含量为百万分之47。
按例1同样的方式将该合金制成永久磁铁,测定其磁性能。结果,其剩余磁通密度4πIr为12.1千高斯,矫顽磁力iHc为10.7千奥斯特,最大能量乘积〔BH〕最大为34.3兆高斯奥斯特。该样品的氧含量为百万分之4400,钙含量为0.02重量%。
例8准备好406克的氟化钕粉、48.6克氟化镝粉、173克10目以下的金属钙粉(所需按化学计算重量的1.25倍)、578克32目以下的铁粉、55克32目以下的铁硼合金粉(20重量%的硼,其余为铁)、30克32目以下的铁铌合金粉(60重量%的铌,其余为铁)、384克氯化钙粉(应生成的氟化钙按化学计算的克分子的1.0倍),将这些原料在V型混合机中混合,以制备1674.6克母料。将此母料装入铁质容器中,在1180℃下的氩气气氛中加热4小时。冷却之后,用酒精水溶液清除熔渣,用酒精冲洗生成的合金,然后在真空中干燥。在室温下通入氢气,使合金吸收氢气。通过氢的吸收完成粉化工序之后用氩气吹除氢气,然后将合金进一步在400℃下进行去氢处理,历时1小时。对合金成分的分析表明,该合金含29.7重量%的钕,3.7重量%的镝,1.0重量%的硼,1.8重量%的铌,0.02重量%的钙,其余为铁。氧含量为百万分之1500,氢含量为百万分之16000。
将此合金用喷磨机磨碎,以制取平均粒度为3.0微米的细粉料。然后将此细粉料在10千奥斯特磁场中以2吨/平方厘米进行压制,将生成的绿色物体在1090℃下的真空中烧结1小时。最后,在900℃下对烧结过的物体进行2小时热处理,然后以1℃/分的速度冷却至室温。再在600℃下加热5小时,然后浸渍在水中快速淬冷。对得出的样品就其磁性能进行测定的结果表明,该样品的剩余磁通密度4πIr=11.5千高斯,矫顽磁力bHc=11.0千奥斯特,iHc=19.5千奥斯特,最大能量乘积〔BH〕最大=31.7兆高斯奥斯特。该样品含百万分之5200的氧,0.02重量%的钙。
例9准备好340克氟化钕粉、124克氟化镝粉、174克10目以下的金属钙粉(所需按化学计算重量的1.25倍)、573克32目以下的铁粉、54克32目以下的铁硼合金粉(20重量%的硼,其余为铁)、29克32目以下的铁铌合金粉(60重量%的铌,其余为铁)和241克的氯化钙粉(应生成的氟化钙按化学计算的克分子的0.5倍)、104克氯化钾粉(应生成的氟化钙按化学计算的克分子的0.8倍)、104克氯化钾粉(应生成的氟化钙按化学计算的克分子的0.8倍)和122克氯化钠粉(应生成的氟化钙按化学计算的克分子的1.2倍),将这些原料在V型混合机中混合,以制备母料。将此母料装入不锈钢容器中,并在1200℃下的氩气气氛中加热2小时。从熔渣中分离出生成的合金之后,令容器倾斜,使合金流入锭型中。于是提出988克合金。对合金成分的分析表明,该合金含有24.6重量%的钕,9.2重量%的镝,1.1重量%的硼,1.8重量%的铌,0.03重量%的钙,其余为铁。
将此合金粉碎,并按例8同样的方式制成,永久磁铁,测定其磁性能。结果,其剩余磁通密度4πIr为10.9千高斯,矫顽磁力bHc为10.3千奥斯特,iHc为25.19千奥斯特,最大能量乘积〔BH〕最大为28.2兆高斯奥斯特。该样品的氧含量为百万分之4800,钙含量0.03重量%。
例10准备好449克的氟化钕粉、13克的氟化镝粉、224克的氢化钙粉(所需按化学计算重量的1.5倍)、569克32目以下的铁粉、54克10目以下的铁硼合金粉、30克10目以下的铁铌合金粉(60重量%铌,其余为铁)、393克氯化钙粉(应生成的氟化钙按化学计算的克分子的1.0倍)、将这些原料在V型混合机中混合,以制备1732克母料。将此母料装入钽容器中,并在1200℃下的氩气气氛中加热4小时。还原反应完成之后,用酒精水溶液清洗熔渣,按例8同样的氢吸收方式粉化生成的合金,以提供985克的粗粉化合金。对合金成分的分析表明,该合金含32.7重量%的钕,1.0重量%的镝,1.1重量%的硼,1.8重量%的铌,0.01重量%的钙,其余为铁。氧含量为百万分之1300。
按例8同样的方式将此合金制成永久磁铁。对得出的合金就其磁性能进行测定的结果表明,其剩余磁通密度4πIr=12.4千高斯,矫顽磁力bHc=11.8千奥斯特,iHc=14.9千奥斯特,最大能量乘积〔BH〕最大=35.8兆高斯奥斯特。该样品含百万分之3700的氧和0.01重量%的钙。
例11准备好418克的氟化钕粉、54克的氟化镝粉、252克10目以下的金属钙粉(所需按化学计算重量的1.75倍)、608克32目以下的铁粉、12克32目以下的硼粉、30克32目以下的铁铌合金粉(60重量%铌,其余为铁)和105克氯化钠粉(应生成的氟化钙按化学计算的克分子的0.5倍),将这些原料在V型混合机中混合,以制备1479克母料。将此母料装入铁容器中,并在例8同样的条件下加热。从熔渣中分离出生成的合金之后,令容器倾斜,使合金流入锭型中。于是得出980克合金。对合金成分的分析表明,该合金含30.0重量%的铌,4.0重量%的镝、1.2重量%的硼,1.8重量%的铌,0.02重量%的钙,其余为铁。氧含量为百万分之70。
按例8同样的方式将此锭坯粉碎并制成永久磁铁,测定其磁性能。结果,其剩余磁通密度4πIr为11.3千高斯,矫顽磁力bHc10.9千奥斯特和iHc20.0千奥斯特,最大能量乘积〔BH〕最大29.6兆高斯奥斯特。该样品的氧含量为百万分之4700,钙含量为0.02重量%。
例12从此实例中可以看到还原剂量与类型之间的关系以及生成的合金的钙含量与由其制备出来的永久磁铁的磁性能之间的关系。
制造程序与例1相同,还原剂采用金属钙和氢化钙,得出含36.0重量%钕、1.3重量%硼、其余为铁的钕铁硼合金。还原剂的用量为氟化钕还原反应所按需化这计算重量的0.8~3.0倍。结果如表一所示。
从表一可知,还原剂的加入量为还原反应表一还原剂量(重量倍数)合金组成 还原剂 项目 0.8 0.9 1.0 1.5 2.0 2.5 3.0钙含量(重量%)0.01 0.02 0.02 0.02 0.02 0.03 0.05钕 金属钙 4πIr36.0重量% (千高斯)13.0 12.7 12.1 12.1 12.1 11.7 11.2硼 iHc1.3重量% (千奥斯特)5.2 8.0 11.0 11.0 11.0 10.0 8.8铁 钙含量其余部分 (重量%)0.01 0.02 0.02 0.02 0.02 0.03 0.05氢化钙 4πIr〔千高斯〕12.9 12.7 12.1 12.1 12.1 11.8 11.0iHc(千奥斯特)5.4 7.8 11.0 11.0 11.0 10.2 9.0所需按化学计算重量的1.0倍或以上时,可使合金产品的钙含量低,且使永久磁铁具有良好的磁性能。看来还原剂使用量最好为化学计算重量的1.0~2.0倍。
例13从此实例中可以看到还原剂量与类型之间的关系,以及生成的合金钙含量与由其制备出来的永久磁铁性能之间的关系。
按例12同样的测量的方法对含29.7重量%钕、3.7重量%镝、1.3重量%硼、1.8重量%铌、其余为铁的钕镝铁硼铌合金进行测量,测量结果示于表二。
表二还原剂量(重量倍数)合金组成 还原剂 项目 0.8 0.9 1.0 1.5 2.0 2.5 3.0钙含量(重量%)0.01 0.02 0.02 0.02 0.02 0.03 0.05钕 金属钙 4πIr29.7重量% (千高斯)11.8 11.5 10.9 10.9 10.9 10.5 10.1镝 iHc3.7重量% (千奥斯特)10.5 12.8 17.0 18.0 17.5 17.0 13.0硼 钙含量1.3重量% (重量%)0.01 0.02 0.02 0.02 0.02 0.03 0.05铌 氢化钙 4πIr1.8重量% 〔千高斯〕11.7 11.5 10.9 10.9 10.9 10.5 10.1铁 iHc其余部分 (千奥斯特)12.5 13.7 18.0 18.7 17.5 17.0 13.1例14从此实例可看到助熔剂量(克分子倍数)与熔渣从合金中分离之间的关系。
按例1同样的程序用其量为氟化钕还原反应以生成氟化钙所需克分子的0.3~0.4倍各种类型的助熔剂混合物制取含41.0重量%钕、1.2重量%硼、其余为铁的钕铁硼合金,结果示于表三。
表三助熔剂 加热温度 助熔剂量(克分子倍数)合金组成 类型 (℃) 0.3 0.4 0.5 1.0 2.0 4.0钕 1,000 不分离 不分离 分离 分离 分离 分离41.0重量% 氯化钙 1,200 不分离 不分离 分离 分离 分离 分离硼 1,000 不分离 不分离 分离 分离 分离 分离1.2重量% 氯化钠 1,200 不分离 不分离 分离 分离 分离 分离铁 1,000 不分离 不分离 分离 分离 分离 分离其余部分 氯化钾 1,200 不分离 不分离 分离 分离 分离 分离从表三可知,为确保熔渣在本系统中能从生成的合金中分离出来,助熔剂量以0.5倍或以上(以克分子计)为宜。
例15从此实例中也可以看到助熔剂量(克分子倍数)与熔渣从合金中的分离之间的关系。
按例14同样的测定方式对含38.0重量%钕、3.7重量%镝、1.3重量%硼、1.8重量%铌、其余为铁的钕镝铁硼铌合金进行测定,其结果如表四所示。
表四助熔剂 加热温度 助熔剂量(克分子倍数)合金组成 类型 (℃) 0.02 0.03 0.05 1.0 2.0 4.0钕 1,00 不分离 不分离 分离 分离 分离 分离38.0重量% 氯化钙 1,200 不分离 不分离 分离 分离 分离 分离镝 1,000 不分离 不分离 分离 分离 分离 分离3.7重量%氯化钠 1,200 不分离 不分离 分离 分离 分离 分离硼 1,000 不分离 不分离 分离 分离 分离 分离1.3重量% 氯化钾 1,200 不分离 不分离 分离 分离 分离 分离铌1.8重量%其余为铁例16从此实例可以看出加热温度与合金从熔渣中分离之间的关系。
按例1同样的程序在900℃和1350℃各种加热温度之间采用各种类型和量的助熔剂混合物制取含38.0重量%钕、1.2重量%硼、其余为铁的钕铁硼合金,结果如表五所示。
表五助熔剂 量(克分 加热温度(℃)合金组成 类型 子倍数) 900 950 1000 1150 1300 1350钕 0.5 不分离 不分离 分离 分离 分离 分离38.0重量% 氯化钙 2.0 不分离 不分离 分离 分离 分离 分离硼 0.5 不分离 不分离 分离 分离 分离 分离1.2重量% 氯化钠 2.0 不分离 不分离 分离 分离 分离 分离铁 0.5 不分离 不分离 分离 分离 分离 分离其余部分 氯化钾 2.0 不分离 不分离 分离 分离 分离 分离从表五可知,加热温度在1000℃或以上确保合金从熔渣中分离出来。
例17从此实例中也可以看出加热温度与合金从熔渣中的分离之间的关系。
按例16同样的方式对含35.5重量%钕、4.6重量%镝、1.0重量%硼、1.1重量%铌、其余为铁的钕镝铁硼铌合金进行测定,结果如表六所示。
表六助熔剂 量(克分 加热温度(℃)合金组成 类型 子倍数) 900 950 1000 1150 1300 1350钕 0.03 不分离 不分离 分离 分离 分离 分离35.5重量% 氯化钙 4.0 不分离 不分离 分离 分离 分离 分离镝 0.03 不分离 不分离 分离 分离 分离 分离4.6重量% 氯化钠 4.0 不分离 不分离 分离 分离 分离 分离硼 0.03 不分离 不分离 分离 分离 分离 分离1.0重量% 氯化钾 4.0 不分离 不分离 分离 分离 分离 分离铌1.1重量%其余为铁例18从此实例可以看出加热温度与来自坩埚的杂质量之间的关系。
按例1同样的程序采用不锈钢坩埚在1000℃和1400℃之间的各种加热温度下制造含36.0%重量%钕、1.3重量%硼、其余为铁的钕铁硼合金,结果如表七所示。
表七助熔器 加热温度(℃)合金组成 类型 项目 1,000 1,150 1,250 1,300 1,350 1,400钕 镍含量36.0重量% 氯化钙(重量%) <0.01 <0.01 <0.01 <0.01 0.23 0.61硼 1.0倍 铬含量1.3重量%(以克(重量%)<0.01 <0.01 <0.01 <0.01 0.12 0.33铁 分子 4πIr(千高斯)12.1 12.1 12.1 12.1 11.4 10.2其余部分 计) iHr(千奥 11.0 11.0 11.0 11.0 9.3 6.8斯特)从表七可知,当加热温度超过1300℃时,镍和铬之类的杂质以大到不能接受的量转移到生成的合金中。
例19从此实例也可以看出加热温度与来自坩埚的杂质量之间的关系。
按例18同样的方式对含29.5重量%钕、6.0重量%镝、1.5重量%、1.3重量%铌、其余为铁的钕镝铁硼铌合金进行测定,结果示于表八。
表八助熔器 加热温度(℃)合金组成 类型 项目 1,000 1,150 1,250 1,300 1,350 1,400钕 镍含量29.5重量% 氯化钙(重量%)<0.01 <0.01 <0.01 <0.01 0.21 0.58镝 1.2倍 铬含量6.0重量% (以克(重量%)<0.01 <0.01 <0.01 <0.01 0.13 0.31硼 分子 4πIn(千高斯) 12.3 12.3 12.3 12.3 11.5 10.41.5重量% 计) iHr(千奥 10.8 10.8 10.8 10.8 9.0 6.5铌 斯特)1.3重量%其余为铁对比实例1在氩气氛中熔化43.2克金属钕、69.0克纯铁和7.8克铁硼合金粉(20.4重量%硼,其余为铁),由此得出118.5克合金。对合金成分进行的分析表明,该合金含35.8重量%的钕、1.30重量%的硼、0.004重量%的钙,其余为铁。氧含量为百万分之48。按例1同样的方式将此合金制成永久磁铁,测定其磁性能。结果,其剩余磁通密度4πIr为12.0千高斯,矫顽磁力iHc为11.2千奥斯特,最大能量乘积〔BH〕最大为34.2兆高斯奥斯特。该样品的氧含量为百万分之4400,钙含量为0.004重量%。
对比实例2准备好125.9克的氧化钕粉、56.2克10目下的金属钙(所需按化学计算重量的1.25倍)、172.3克100目以的铁粉和19.8克100目以下的铁硼合金粉(20.4重量%硼,其余为铁),将这些原料V型混合机中混合,以制备374.2克母料。将此母料装入不锈钢容器中,并在1200℃下的氩气氛中加热4小时,以便进行还原反应。
然后将反应生成物倒入水中,反复清洗以除去所生成的氧化钙。如此得出的粗粉末其干重为288.0克。对该粗粉末进行的组成分析表明,该粉末含35.4重量%的钕、1.30重量%的硼、0.25重量%的钙,其余为铁。氧含量为百万分之6000。
按例1同样的方式将该合金粉化成细粉、压制、烧结和热处理,以制成永久磁铁,然后测定其磁性能。结果,其剩余磁通密度4πIr为11.8千高斯,矫顽磁力iHc为8.5千奥斯特,最大能量乘积〔BH〕最大为32.0兆高斯奥斯特。该样品的氧含量为百万分之9000,钙含量为0.25重量%。
对比实例3准备好209.2克氟化钕粉、78.2克10目以下的金属钙(所需按化学计算重量的1.25倍)、50.0克32目以下的铁粉和172.8克的氯化钙粉(应生成的氟化钙按化学计算的克分子的1.0倍),将这些原料在V型混合机中混合,以制备510.2克母料。将此母料装入不锈钢容器中,并在900℃下的氩气气氛中加热1小时。从熔渣中分离出生成的合金之后,令容器倾斜,使合金流入锭型中。于是得出194.0克合金。对合金组成的分析表明,该合金含74.8重量%的钕、0.35重量%的钙,其余为铁。氧含量为百万分之75。取57.8克该合金与54.6克纯铁及7.8克铁硼合金(20.4重量%的硼,其余为铁)混合,将得出的混合物在氩气氛中用电弧熔化。在熔化过程中产生大量钙气,污染了所用炉子的内壁。由此得出117.8克合金。对此合金的分析表明,该合金含35.7重量%的钕、1.29重量%的硼、0.08重量%的钙,其余为铁。氧含量为百万分之55。按例1同样的方式将该合金制成永久磁铁,然后测定其磁性能。结果,其剩余磁通密度4πIr为11.9千高斯,矫顽磁力iHc为10.7千奥斯特,最大能量乘积〔BH〕最大为33.5兆高斯奥斯特。该样品的氧含量为百万分之4600,钙含量为0.08重量%。
对比实例4将336克氧化钕粉、64克氧化镝粉、183克10目以下的金属钙粉(所需按化学计算重量的1.25倍)、11克32目以下的硼粉、29克32目以下的铁铌合金(60重量%铌,其余为铁)和605克100目以下铁粉混合起来,制备1228克母料。将此母料装进铁容器中,并在1200℃下的氩气氛中加热4小时,以便进行还原反应。
然后将反应生成物倒入水中,反复清洗,以除去所生成的氧化钙。于是得出干重为930克的粗粉。对此粗粉组成的分析表明,该粗粉含29.5重量%的钕,3.6重量%的镝,1.1重量%的硼,1.8重量%的铌,0.27重量%的钙,其余为铁。氧含量为百万分之7000。
按实例8同样的方式将此粗合金粉磨碎、压制、烧结和热处理,制成永久磁铁,然后测定其磁性能。结果,其剩余磁通密度4πIr为11.0千高斯,矫顽磁力bHc为10.3千奥斯特,iHc为14.5千奥斯特,最大能量乘积〔BH〕最大为28.3兆高斯奥斯特。该样品的氧含量为百万分之9500,钙含量为0.25重量%。
如上面所详细介绍的那样,本发明的方法能以低成本提供钙含量和氧含量极低磁性能充分可以接受的钕铁硼永久磁铁合金。
本发明已经通过上述诸实例介绍过了。但应该指出的是,这些实例不是旨在限制本发明,任何修改只要不脱离本说明书所附各项
权利要求
1.一种生产基本上由25.0~50.0重量%的钕、0.3~5.0重量%的硼、其余大体上为铁所组成的钕铁硼永久磁铁合金的方法,其特征在于,该方法包括下列诸工序往氟化钕、铁和硼(或铁硼合金)中加入作为还原剂的金属钙、氢化钙或它们的混合物,再加入作为助熔剂的氯化钙、氯化钠和氯化钾中的至少一种,将得出的混合物在1,000~1,300℃下的惰性气体气氛中或还原气体气氛中或大体上真空中熔化,从而还原所述氟化钕,以制取钙含量极低的所述合金。
2.根据权利要求
1生产钕铁硼永久磁铁合金的方法,其特征在于,作为还原剂的金属钙、氢化钙或它们的混物,其加入量为所述氟化钕还原反应所需按化学计算加入量的1.0~4.0倍(以重量计)。
3.根据权利要求
1生产钕铁硼永久磁铁合金的方法,其特征在于,作为助熔剂的氯化钙、氯化钠和氯化钾中的至少一种,其加入量为由所述氟化钕还原反应生成氟化钙所需按化学计算加入量的0.05~4.0倍(以克分子计)。
4.根据权利要求
1生产钕铁硼永久磁铁合金的方法,其特征在于,生成的合金中的钙含量为0.1重量%或以下。
5.一种生产基本上由25.0~50.0重量%钕、0.5~15.0重量%镝、0.3~5.0重量%硼、0.05~5.0重量%铌、其余大体上为铁所组成的钕镝铁硼铌永久磁铁合金的方法,其特征在于,该方法包括下列诸工序往氟化钕、氟化镝、铁、硼(或铁硼合金)和铌(或铁铌合金)中加入作为还原剂的金属钙、氢化钙或它们的混合物,再加入作为助熔剂的氯化钙、氯化钠和氯化钾中的至少一种,将得出的混合物在1,000~1,300℃下的惰性气体气氛中或还原气体气氛中或大体上真空中熔化,从而还原所述氟化钕和所述氟化镝,以制取钙含量极低的所述合金。
6.根据权利要求
5生产钕镝铁硼铌永久磁铁合金的方法,其特征在于,作为还原剂的金属钙、氢化钙或它们的混合物,其加入量为所述氟化钕和所述氟化镝还原反应所需加入量的按化学计算量的1.0~4.0(以重量计)。
7.根据权利要求
5生产钕镝铁硼铌永久磁铁合金的方法,其特征在于,作为助熔剂的氯化钙、氯化钠和氯化钾中的至少一种,其加入量为由所述氟化钕和氟化镝的还原反应生成氟化钙所需加入量按化学计算量的0.05~4.0倍(以克分子计)。
8.根据权利要求
5生产钕镝铁硼铌永久磁铁合金的方法,其特征在于,生成的合金中的钙含量为0.1重量%以下。
一种生产基本上由25.0~50.0重量%的钕、0.3~5.0重量%的硼、其余大体上为铁所组成的钕铁硼永久磁铁合金的方法,该方法包括下列诸工序往氟化钕、铁和硼(或铁硼合金)中加入作为还原剂的金属钙、氢化钙或它们的混合物,再加入作为助熔剂的氯化钙、氯化钠和氯化钾中的至少一种,将得出的混合物在1,000~1,300℃下的惰性气体气氛中或还原气体气氛中或大体上真空中熔化,从而还原所述氟化钕以制取钙含量低到0.1重量%或以下的所述合金。
生产钕铁硼永久磁铁的方法
- 专利详情
- 全文pdf
- 权力要求
- 说明书
- 法律状态
查看更多专利详情
下载专利文献
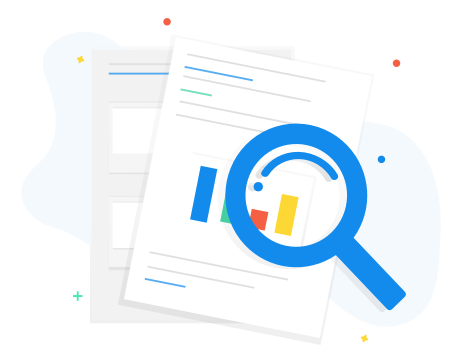
下载专利
同类推荐
-
张亚锋, 胡长坤王志远崔桂玲
您可能感兴趣的专利
-
崔桂玲崔桂玲崔桂玲崔桂玲崔桂玲崔桂玲
专利相关信息
-
陈春雷, 施绍安陈春雷, 施绍安王卫刚王卫刚王卫刚王卫刚