专利名称:一种铝电解槽用阴极炭块的生产方法 目前,铝电解槽所使用的阴极炭块基本上分为两类。一类阴极炭块是以电煅无烟煤为主要原料,添加不同含量的人造石墨碎,加入煤沥青作为粘结剂,通过“破碎→筛分→配料→混捏→成型→焙烧→加工工序”,而生产的半石墨质阴极炭块。该种生产工艺需要的人造石墨碎数量有限,且质量不易控制,不仅影响产品质量,且限制产品数量。另一类阴极炭块是采用煅后石油焦为主要原料,加入煤沥青作为粘结剂,通过“破碎→筛分→配料→混捏→成型→一次焙烧→浸渍→二次焙烧→石墨化→加工工序”而生产的全石墨化阴极炭块。半石墨质阴极炭块抗钠侵蚀能力差,炉底压降高;全石墨化阴极炭块的生产工艺流程长,能耗高,价格贵,并且产品的抗磨性差。这两种产品都不利于延长电解槽寿命。
本发明的目的是针对上述已有技术的不足,提供一种能够有效缩短生产工艺流程,降低生产成本,其产品性能适合铝电解槽要求的阴极炭块的生产方法。本发明的方法是通过以下技术方案实现的。一种铝电解槽用阴极炭块的生产方法,其特征在于该方法包括a.破碎→筛分→配料→混捏→成型→一次焙烧→浸渍→二次焙烧→加工工序;b.阴极糊料中按重量百分比选用半石墨化石油焦为10%-80%,以颗粒、粉料形式加入,全石墨化石油焦为10%-80%,以颗粒、粉料形式加入,电煅无烟煤为10%-50%,以颗粒形式加入,焙烧碎为0%-10%,以颗粒形式加入作为骨料,选用含煤焦油0%-30%的调质煤沥青作为粘结剂,其骨料占糊料(重量百分比)的80%-85%,其粘结剂占糊料的15%-20%;c.混捏温度为130-180;d.成型温度为110℃-150℃;e.一次焙烧温度为700℃-1000℃;f.二次焙烧温度为1100℃-1300℃。本发明的一种铝电解槽用阴极炭块的生产方法,其特征在于生产半石墨化石油焦和全石墨化石油焦时添加(重量百分比)1%-10%氧化硼或碳化硼或铝硅酸盐作为催化石墨化添加剂。本发明的一种铝电解槽用阴极炭块的生产方法,其特征在于生产电煅无烟煤时添加(重量百分比)1%-10%氧化硼或碳化硼或铝硅酸盐作为催化石墨化添加剂。由于采用了上述技术方案,本发明具有生产工艺流程短,生产成本低,其产品性能真密度2.10-2.20g/cm3,体积密度1.56-1.65g/cm3,电阻率16-36μΩm,热导率25-45W/mK,抗压强度20-38MPa,抗折强度3-7MPa。
下面结合实施例来对本发明的方法做进一步的说明。
一种铝电解槽用阴极炭块的生产方法,其特征在于该方法包括a.破碎→筛分→配料→混捏→成型→一次焙烧→浸渍→二次焙烧→加工工序;b.阴极糊料中按重量百分比选用半石墨化石油焦为10%-80%,以颗粒形式加入,全石墨化石油焦为10%-80%,以颗粒、粉料形式加入,电煅无烟煤为10%-50%,以颗粒形式加入,焙烧碎为0%-10%,以颗粒形式加入作为骨料,选用含煤焦油0%-30%的调质煤沥青作为粘结剂,其骨料占糊料(重量百分比)的80%-85%,其粘结剂占糊料的15%-20%。c.混捏温度为130℃-180℃;d.成型温度为110℃-150℃;e.一次焙烧温度为700℃-1000℃;f.二次焙烧温度为1100℃-1300℃。半石墨化石油焦和全石墨化石油焦添加(重量百分比)1%-10%氧化硼或铝硅酸盐添加剂。电煅无烟煤添加(重量百分比)1%-10%氧化硼或铝硅酸盐添加剂。
实施例1在阴极糊料中加入以1%的碳化硼作为添加剂而生产的全石墨化石油焦(重量百分比)30%,以粉料形式加入;半石墨化石油焦为40%,以颗粒、粉料形式加入;电煅无烟煤为13%,以颗粒形式加入;加入17%含0%煤焦油的调质煤沥青为粘结剂;混捏温度165℃,成型温度150℃,一次焙烧温度750℃,二次焙烧温度1200℃。所得产品的钠膨胀系数为0.55%,电阻率为16μΩm,其他性能指标满足要求。
实施例2在阴极糊料中加入以1%的铝硅酸盐作为添加剂而生产的全石墨化石油焦(重量百分比)40%,以粉料形式加入;半石墨化石油焦为20%,电煅无烟煤为23%,焙烧碎为2%,均以颗粒形式加入;以含10%煤焦油的调质煤沥青为粘结剂,加入量为15%;混捏温度160℃,成型温度145℃,一次焙烧温度800℃,二次焙烧温度1250℃。所得产品的钠膨胀系数为0.50%,电阻率为26μΩm,其他性能指标满足要求。
实施例3在阴极糊料中加入以5%的氧化硼作为添加剂而生产的全石墨化石油焦(重量百分比)50%,以小颗粒、粉料加入;电煅无烟煤为32%,以颗粒、粉料形式加入;以含30%煤焦油调质煤沥青为粘结剂,加入量为18%;混捏温度150℃,成型温度140℃,一次焙烧温度850℃,二次焙烧温度1150℃。所得产品的钠膨胀系数为0.40%,电阻率为32μΩm,其他性能指标满足要求。
实施例4在阴极糊料中加入以8%的铝硅酸盐作为添加剂而生产的全石墨化石油焦(重量百分比)70%,以颗粒、粉料形式加入;电煅无烟煤为15%,以颗粒形式加入;加入15%含20%煤焦油调质煤沥青为粘结剂;混捏温度155℃,成型温度为145℃,一次焙烧温度为850℃,二次焙烧温度1200℃。所得产品的钠膨胀系数为0.30%,电阻率为34μΩm,其他性能指标满足要求。
实施例5在阴极糊料中加入以5%的氧化硼作为添加剂而生产的半石墨化石油焦(重量百分比)50%,以颗粒、粉料加入;全石墨化石油焦为20%,以粉料形式加入;电煅无烟煤为10%,以颗粒形式加入;加入20%含30%煤焦油的调质煤沥青为粘结剂,混捏温度155℃,成型温度140℃,一次焙烧温度900℃,二次焙烧温度1250℃。所得产品的钠膨胀系数为0.30%,电阻率为20μΩm,其他性能指标满足要求。
实施例6在阴极糊料中加入以8%的铝硅酸盐作为添加剂而生产的半石墨化石油焦为(重量百分比)70%,以颗粒、粉料形式加入;电煅无烟煤为13%,以颗粒形式加入;加入17%含15%煤焦油的调质煤沥青为粘结剂,混捏温度160℃,成型温度150℃,一次焙烧温度950℃,二次焙烧温度1250℃。所得产品的钠膨胀系数为0.25%,电阻率为36μΩm,其他性能指标满足要求。
实施例7在阴极糊料中加入以5%的氧化硼作为添加剂而生产的电煅无烟煤为(重量百分比)50%,以颗粒、粉料形式加入;全石墨化石油焦为30%,以粉料形式加入; 焙烧碎为3%,以颗粒形式加入;加入17%含0%煤焦油的调质煤沥青为粘结剂;混捏温度170℃,成型温度150℃,一次焙烧温度750℃,二次焙烧温度1200℃。所得产品的钠膨胀系数为0.55%,电阻率为24μΩm,其他性能指标满足要求。
实施例8在阴极糊料中加入以3%的碳化硼作为添加剂而生产的半石墨化石油焦为(重量百分比)40%,以粉料形式加入;焙烧碎为9%,以颗粒形式加入;电煅无烟煤31%,以颗粒形式加入;加入20%含0%煤焦油的调质煤沥青为粘结剂;混捏温度1250℃,成型温度115℃,一次焙烧温度900℃,二次焙烧温度1350℃。所得产品的钠膨胀系数为0.55%,电阻率为24μΩm,其他性能指标满足要求。
一种铝电解槽用阴极炭块的生产方法,其特征在于包括破碎→筛分→配料→混捏→成型→一次焙烧→浸渍→二次焙烧→加工工序;阴极糊料中按重量百分比选用半石墨化石油焦为10%-80%,以颗粒、粉料形式加入,全石墨化石油焦为10%-80%,以颗粒、粉料形式加入,电煅无烟煤为10%-50%,以颗粒形式加入,焙烧碎为0%-10%,以颗粒形式加入作为骨料,选用含煤焦油0%-30%的调质煤沥青作为粘结剂,其骨料占糊料(重量百分比)的80%-85%,其粘结剂占糊料的15%-20%。混捏温度为130℃-180℃;成型温度为110℃-150℃;一次焙烧温度为700℃-1000℃;二次焙烧温度为1100℃-1300℃。本发明具有生产工艺流程短,生产成本低,其产品性能指标满足使用要求。
一种铝电解槽用阴极炭块的生产方法
- 专利详情
- 全文pdf
- 权力要求
- 说明书
- 法律状态
查看更多专利详情
下载专利文献
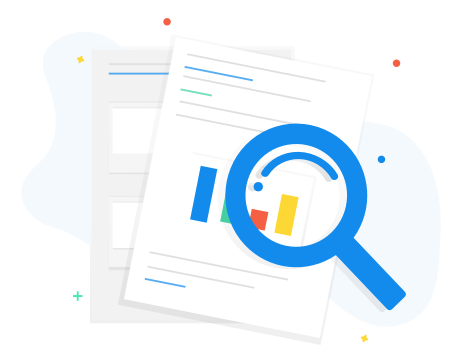
下载专利
同类推荐
-
张亚锋, 胡长坤张亚锋, 胡长坤崔桂玲
您可能感兴趣的专利
-
崔桂玲崔桂玲崔桂玲崔桂玲崔桂玲崔桂玲陈春雷, 施绍安
专利相关信息
-
陈春雷, 施绍安王卫刚王卫刚K·梁K·梁K·梁