一种高强耐磨复相多晶工程板的生产方法【技术领域】[0001]本发明涉及一种人造石材或部分工程材料的生产【技术领域】,也涉及化工、冶金、建筑装饰、石油等【技术领域】。[0002]在建筑领域,天然石材作为一种不可再生资源,更需特别关注。我国非金属矿产资源储量在世界排名里居中,就是说并不是很非富。天然石材生成年代漫长,属于不可再生资源。但是随着国家建设及各方面需求量增加,天然石材的使用却日渐普遍。尤其在建筑装饰方面,因而高效 、合理地综合利用,会为国家节省更多的宝贵天然资源并利于改善生态环境。目前,国内石材开采及加工企业,往往只注意到成荒率、出材率和加工工艺等,而很少关注天然石材的综合利用。有些从事石材矿山开采、生产、加工、施工的人员,甚至包括建筑业内的工程设计者,对天然石材下脚料的利用根本不够重视,一般只当作废品抛弃。天然石材在开采过程中有50%左右变成了非规格毛石和碎石,就全国现有石材荒料产量推算,这可是一个非常可观的数字,若能充分利用,既有经济利益,又能节约资源。在加工天然石材的过程中,将会产生大约为荒料5%,毛板总量1/3左右的边角余料。如果作为废料抛弃,还得付出经济代价运出,堆放不当还有碍环保。石材加工厂的各道工序(锯、磨、切),都产生一些废石浆,如若胡乱排放,相当污染环境。[0003]因此,减少天然石材在开采和加工过程中的损失,除积极采用新技术、新工艺、新设备提高操作者的技术水平和素质之外,最重要的就是进一步开发天然石材的综合利用,变废为宝,变害为利。另一方面,在化工、石油、电力、冶金行业中一些重要装备及关键部件经常面临着高温,急速温差变化,高腐蚀,高磨损,介质遇水炸裂强冲击等一系列极其严酷的工作环境。而目前市场上应用的大理石、铸石、铸铁、锰钢等产品由于自身材质的各种先天性缺陷,使其在实际应用中均难以适应上述工作环境。
[0004]本发明目的在于综合利用固体废弃物提供强度高、耐磨损、抗腐蚀、对人体无放射性危害的复相多晶工程材料的生产方法。[0005]本发明技术方案有两种:
第一种是:将钙基废料、辅助原料、助熔澄清剂和水混合均匀后投入熔窑,经均化、澄清后形成高温熔体,再将高温熔体经过压延或浇注制成基础非晶板,将基础非晶板经过晶化处理形成复相多晶工程板毛坯板;所述钙基废料为石灰石废料或大理石废料或方解石废料;所述辅助原料为石英砂或硅石或纯碱或氧化铝或氧化锌或碳酸钡或碳酸钾或氧化镁或萤石或硝酸钠中的至少四种材料;所述助熔澄清剂为Ce02、Na2O, A1203、SiO2, CaO、Li2O,NH4NO3> NaNO3或Na2SO4中的至少任意一种。
[0006]第二种是:将钙基废料、辅助原料、助熔澄清剂和水混合均匀后投入熔窑,经均化、澄清后形成高温熔体,再将高温熔体经过水淬制成非晶态粒料,将非晶态粒料经过烧结晶化成复相多晶工程板毛坯板;所述钙基废料为石灰石废料或大理石废料或方解石废料;所述辅助原料为石英砂或娃石或纯碱或氧化招或氧化锌或碳酸钡或碳酸钾或氧化镁或萤石或硝酸钠中的至少四种材料;所述助熔澄清剂为Ce02、Na2O, A1203、SiO2, CaO、Li2O, ΝΗ4Ν03、NaNO3或Na2SO4中的至少任意一种。
[0007]本发明以上两种方法都以钙基废料为原料生产高附加值的高强耐磨复相多晶工程板,复相多晶工程板毛坯板出炉之后,采用以上方法可以制作不同颜色和规格的建筑装饰板材,具有独特的高温耐磨性、强力抗高温冲击、耐强烈腐蚀、抗炸裂冲击等性能,制作成水渣沟内衬、耐磨管道制品、布料溜槽以及各种耐磨衬板,可广泛应用于煤炭、钢铁、选矿、电力等行业。对制成的产品进行定厚、粗磨、细抛,切割、倒棱,得到不同规格尺寸和光泽度的成品。
[0008]与现有普通微晶板相比,本发明具有以下有益效果:
1、高强度、耐磨损,优异的物理力学性能及化学稳定性:
本发明的复相多晶工程板的物理力学性能优异,密度2.5-2.8g/cm3,莫氏硬度6_8,抗折强度 30.0-103.5MPa,抗压强度 70.0-903.0MPa,耐磨性 0.063-0.15g/cm2。
[0009]2、组织结构中晶粒尺寸小、晶体含量高:
本发明的钙基废料复相多晶工程材料的组织结构由玻璃相和晶相组成,其中晶相由枪晶石、钙铝黄长石、硅灰石、氟碱钙硅石、钙镁黄长石、碱钙硅石、镁橄榄石、透辉石、莫来石、 白榴石、石英中的一种或一种以上晶体组成,具有极好的高强耐磨性,同时通过调整生产工艺参数调控复相多晶材料中的晶体含量(晶化率)及晶粒尺寸,同时也使钙基废料中的微量元素在调控晶化率、晶粒尺寸及复相多晶材料物理力学性能及化学稳定性方面起到关键的作用。
[0010]3、高值化综合利用钙基废料:
不仅可以降低复相多晶材料的生产成本,还可以减轻固体废弃物对环境的污染。
[0011]本发明中所述钙基废料占钙基废料、辅助原料、助熔澄清剂和水总质量的10.0~
25.0wt%,辅助原料占钙基废料、辅助原料、助熔澄清剂和水总质量的65.0-73.0wt%,助熔澄清剂占钙基废料、辅助原料、助熔澄清剂和水总质量的2.0~10.0Wt%。
[0012]本发明中所述助熔澄清剂中Ce02、Na2O, A1203、SiO2, CaO、Li2O, NH4NO3^ NaNO3 和Na2SO4的质量比为O~5:0~28:0~6:0~10:0~11:0~4:1~5:0~7: O ~13。
[0013]本发明中所述钙基废料中CaO占钙基废料总质量的45.0~55%,SiO2占钙基废料总质量的0.01~1.5%,Al2O3占钙基废料总质量的0.01~2.0%,Mg0占钙基废料总质量的
0.01~2.0%,Fe2O3占钙基废料总质量的0.01~2.0%。
[0014]本发明中所述辅助原料中石英砂、硅石、纯碱、氧化铝、氧化锌、碳酸钡、碳酸钾、氧化镁、萤石和硝酸钠的质量比为40~98: 8~35: O~5: O~4: O~5: 5~17:
O ~7: 7 ~14: O ~17。
[0015]另外,本发明所述钙基废料和辅助原料的粒径小于2mm。
[0016]所述熔窑的温度为1400~1560°C (优选1420~1520°C ),在熔窑内的熔化时间为 1.0 ~10.0h (优选 2.0 ~8.0h)。
[0017]可以将温度为1100~1200°C的高温熔体通过对辊压延机压延制成非晶态基础板。
[0018]还可将非晶态基础板进一步破碎成非晶态碎块料。
[0019]也可将温度为1250~1350°C的高温熔体浇注到经预热的模具中成型,得到非晶态的基础板。
[0020]还可将温度为1300~1350°C的高温熔体经过水淬,制成不同粒径的非晶态基础粒料,干燥、分级后待装模使用。
[0021]晶化的方法有两种:
一是:将非晶态基础板经400~650°C退火2.0~8.0h,然后再于650~950°C晶化
1.0~9.0h,最后再于25~600°C退火2.0~8.0h。
[0022]二是:将非晶态基础粒料装模后在梭式窑中,以5~20°C /min的速度升温至1050~1180°C,保温O~2.5h摊平表面,然后以3~15°C /min的速度降至600~950°C,保温1.0~4.0h晶化处理,最后再以2~10°C /min的速度降温至200~700°C,保温1.0~
8.0h退火,制成复相多晶工程板毛坯板。
[0023]下面以实施例具体描述本发明,本发明不受实施例的限制。
[0024]以下实施例中:钙基废料中CaO占钙基废料总质量的45.0~55%,SiO2占钙基废料总质量的0.01~1.5%,Al2O3占钙基废料总质量的0.01~2.0%,Mg0占钙基废料总质量的0.01~2.0%,Fe2O3占钙基废料总质量的0.01~2.0%。
[0025]实施例1:
将钙基废料和各种矿物辅料粉碎,然后过40目筛,称量10.0~25.0千克钙基废料,50.0~67.0千克石英砂或硅石粉(Si02)、8.0~14.0千克纯碱(Na2C03)、0.0_4.0千克氧化铝(A1203)、0~3.0千克氧化锌(Zn0)、9.0~16.0千克碳酸钾(K2C03)、9.0~15.0千克萤石(CaF2)、3.0~5.0千克硝酸钠(NaNO3), 1.0~3.0千克硝酸铵(NH4NO3X将钙基废料、辅助原料及助熔澄清剂充分混合,并在混合过程中加入原材料总重量4.0%的水,搅拌IOmin混合均匀,形成基础配合料。
[0026]将基础配合料经输送带或单元料罐送入熔窑中,熔化温度控制在1460~1490°C熔化2.0~6.0h,经均化、澄清制成合格的高温熔体。澄清的高温熔体经流液洞进入熔窑工作部,温度降至1120~1180°C,高温熔体通过对辊压延机(压延成型速度12.0~25.0m/h)压制成基础非晶板。
[0027]成形的基础非晶板进入辊道窑,首先进入基础非晶板板退火温区,在450~650°C温区内基础非晶板板退火2.0~3.0h,然后进入650~850°C温区,晶化5.0~7.0h,最后进入600~25°C温区,复相多晶工程板退火4.0~6.0h。
[0028]高强耐磨复相多晶工程板毛坯板出炉之后,对其进行定厚、粗磨、细抛,切割、倒棱,得到不同规格尺寸和光泽度的成品。
[0029]实施例2
将钙基废料和各种矿物辅料粉碎,然后过40目筛,称量10.0~25.0千克钙基废料,50.0~67.0千克石英砂或硅石粉(Si02)、8.0~14.0千克纯碱(Na2C03)、0.0-4.0千克氧化铝(A1203)、0~3.0千克氧化锌(Zn0)、9.0~16.0千克碳酸钾(K2C03)、9.0~15.0千克萤石(CaF2)、3.0~5.0千克硝酸钠(NaNO3), 1.0~3.0千克硝酸铵(NH4NO3X将钙基废料、辅助原料及助熔澄清剂充分混合,加入原材料总重量3.0~4.0%的水,搅拌10~15min混合均匀,形成基础配合料。
[0030]将基础配合料经输送带或单元料罐送入熔窑中,熔化温度控制在1470~1530°C熔化2.0~6.0h,经均化、澄清制成合格的高温熔体。澄清的高温熔体经流液洞进入熔窑工作部,温度降至1250-1300°C,高温熔体浇注到经预热的模具中成型,得到基础非晶块。
[0031]浇注成形的基础非晶块送入梭式窑或隧道窑或辊道窑内,在梭式窑内以5°C /min的速度升温至650~950°C保温6.0h晶化,然后以3°C /min的速度降温至200~700°C保温6.0h退火,消除复相多晶工程板在热处理过程中产生的各种应力,随炉冷却。
[0032]高强耐磨复相多晶工程板毛坯板出炉之后,对其进行定厚、粗磨、细抛,切割、倒棱,得到不同规格尺寸和光泽度的成品。
[0033]实施例3
将钙基废料和各种矿物辅料粉碎,然后过40目筛,称量10.0~25.0千克钙基废料,50.0~67.0千克石英砂或硅石粉(Si02)、8.0~14.0千克纯碱(Na2CO3)、0.0~4.0千克氧化铝(A1203)、0~3.0千克氧化锌(Zn0)、9.0~16.0千克碳酸钾(K2C03)、9.0~15.0千克萤石(CaF2)、3.0~5.0千克硝酸钠(NaNO3), 1.0~3.0千克硝酸铵(NH4NO3)15将钙基废料、辅助原料及助熔澄清剂充分混合,加入原材料总重量3.0~4.0%的水,搅拌10~15min混合均匀,形成基础配合料。 [0034]将基础配合料经输送带或单元料罐送入熔窑中,熔化温度控制在1470~1530°C熔化2.0~6.0h,经均化、澄清制成合格的高温熔体。澄清的高温熔体经流液洞进入熔窑工作部,温度降至1320~1350°C (以保证水淬非晶颗粒的粒度均匀),经过平槽流料口或孔形流料口进入循环水槽中,水淬成不同粒径的基础非晶粒料,干燥、分级后待装模使用。
[0035]水淬成的基础非晶粒料按照不同的粒度分层装模后送入梭式窑,或基础非晶板破碎成的尺寸大小不同的碎非晶块料按照不同的尺寸分层装模后送入梭式窑,以5~20°C /min的速度升温至1130~1190°C保温0.5~1.5h摊平表面,然后以5°C /min的速度降至600~970°C保温1.0~4.0h晶化处理,最后再以3°C /min的速度降温在200~700°C保温7.0h退火,制成大花纹型或小花纹型复相多晶工程板毛坯板。
[0036]高强耐磨复相多晶工程板毛坯板出炉之后,对其进行定厚、粗磨、细抛,切割、倒棱,得到不同规格尺寸和光泽度的成品。
一种高强耐磨复相多晶工程板的生产方法
- 专利详情
- 全文pdf
- 权力要求
- 说明书
- 法律状态
查看更多专利详情
下载专利文献
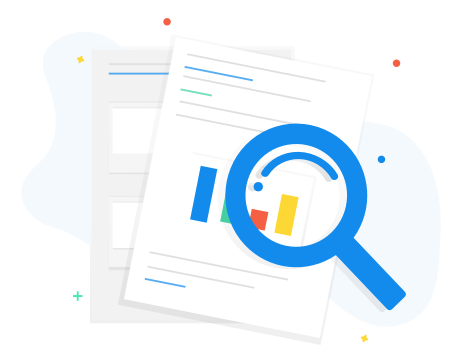
下载专利
同类推荐
-
张亚锋, 胡长坤郭伟明郭伟明郭伟明
您可能感兴趣的专利
-
崔桂玲崔桂玲崔桂玲
专利相关信息
-
崔桂玲崔桂玲崔桂玲崔桂玲